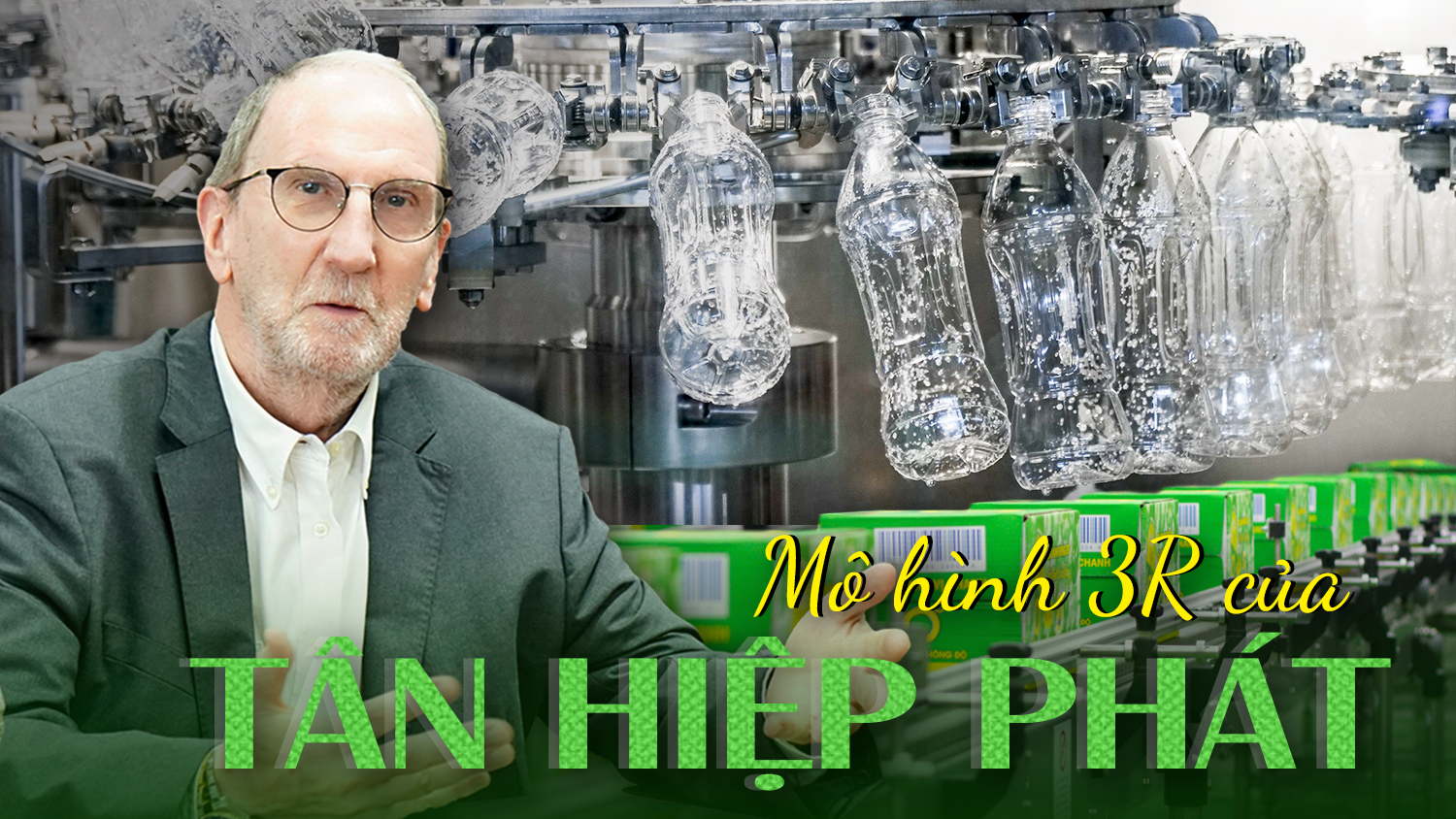
Mô hình 3R của Tân Hiệp Phát trong phát triển kinh tế tuần hoàn
Việc áp dụng mô hình 3R về giảm thiểu chất thải (Reducing waste), tái sử dụng (Reusing) và tái chế (Recycling) trong sản xuất kinh doanh mang lại hiệu quả cao trong việc tiết kiệm nguồn lực, đổi mới quy trình, phát triển sáng tạo, đem đến lợi ích trực tiếp và lợi thế cạnh tranh cho Tân Hiệp Phát.
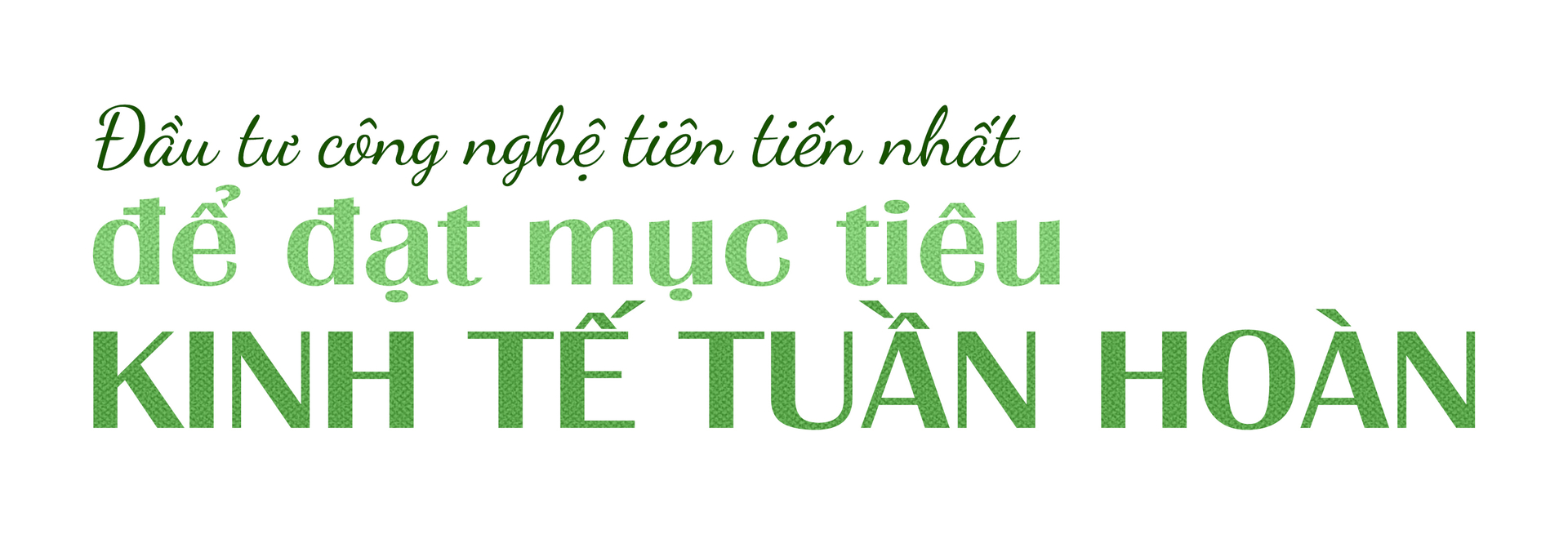
Tân Hiệp Phát (THP) đã đầu tư công nghệ tiên tiến nhất thế giới với khả năng tự động hóa cao nhất để đạt được các mục tiêu kinh tế tuần hoàn (KTTH), bao gồm hiệu quả kinh tế và tuần hoàn tối đa. Được biết đến với công nghệ dây chuyền sản xuất nước giải khát chiết lạnh vô trùng Aseptic, THP từ nhiều năm qua đã đầu tư hệ thống máy móc của hãng GEA Procomac Đức.
Công nghệ chiết lạnh vô trùng giúp tạo ra những sản phẩm có chất lượng tốt nhất và giữ nguyên các giá trị dinh dưỡng trong sản phẩm, đồng thời vẫn đáp ứng các yêu cầu vô trùng nghiêm ngặt. Áp dụng công nghệ này còn giúp THP giảm thiểu lượng nhựa sử dụng trong sản xuất hết mức có thể bằng cách giảm trọng lượng của chai nhựa.
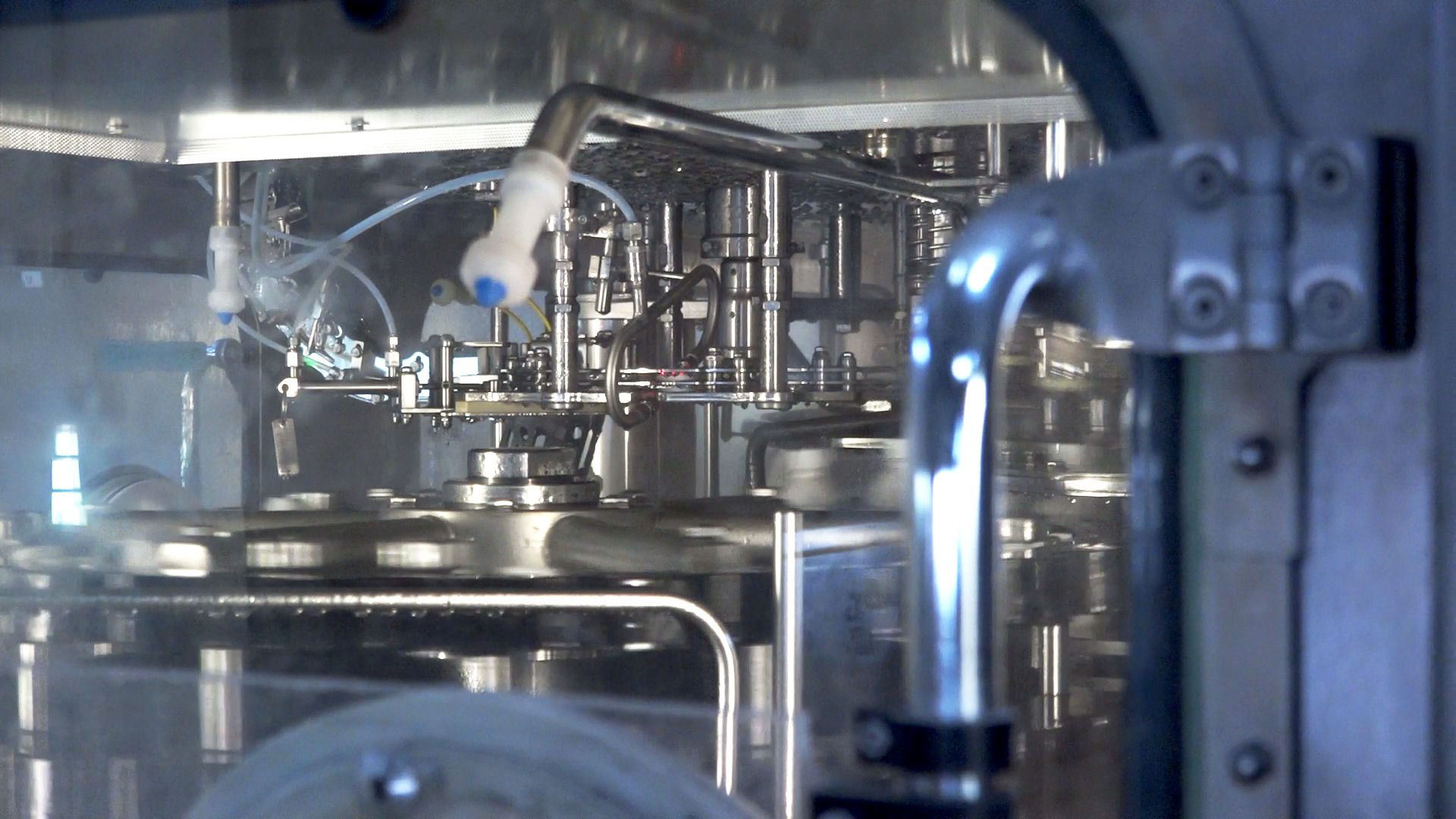
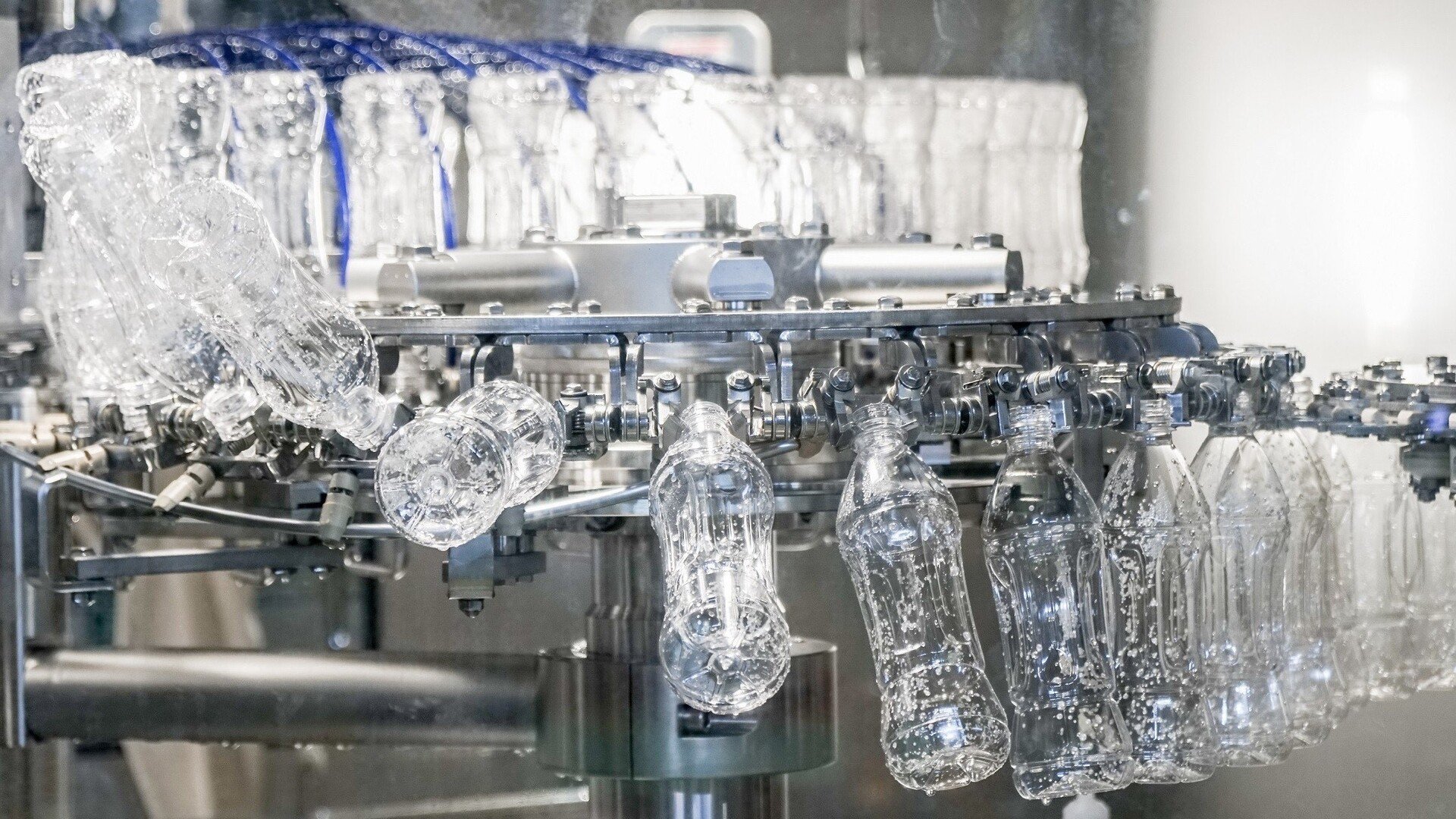
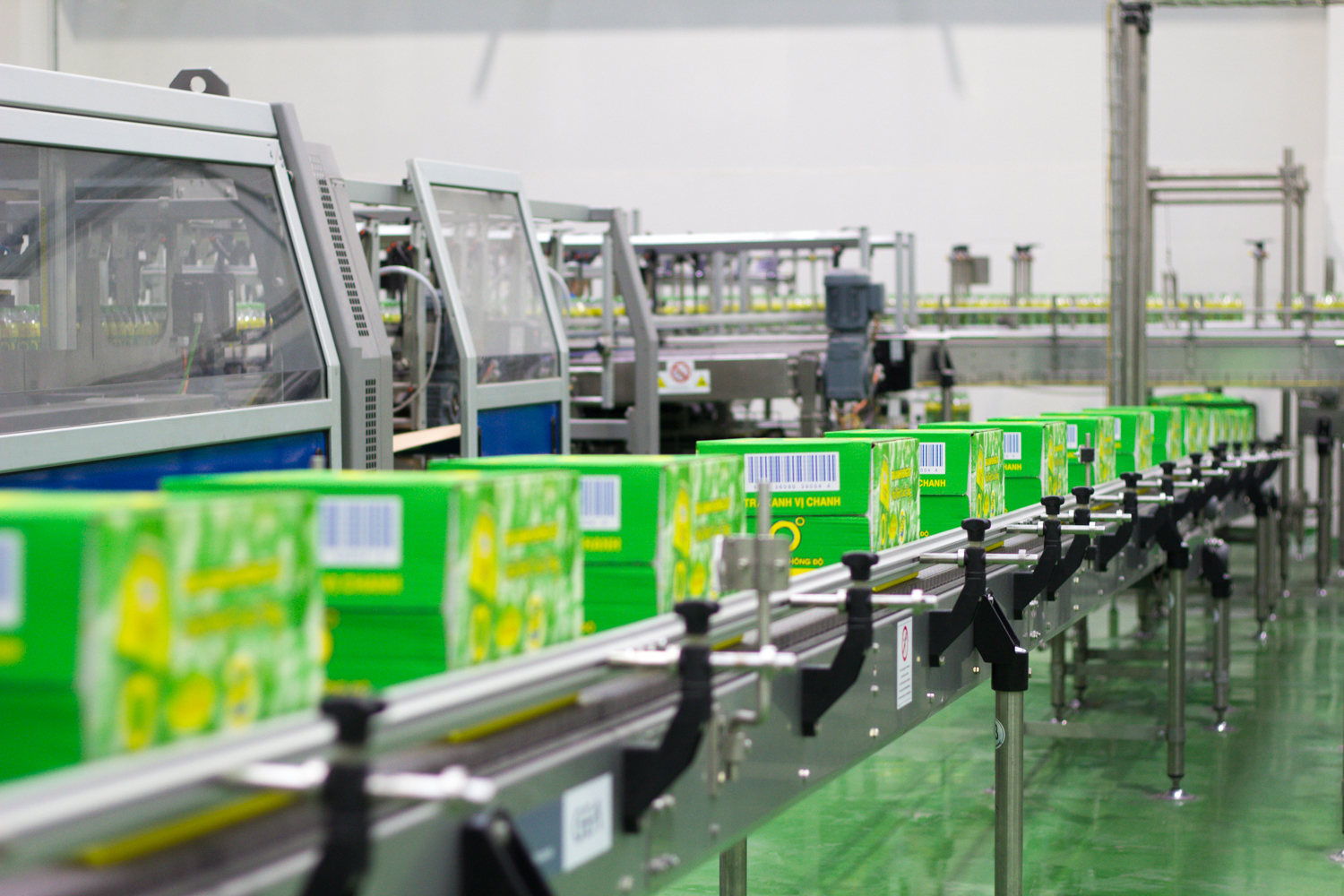
Tân Hiệp Phát đã đầu tư công nghệ tiên tiến nhất thế giới với khả năng tự động hóa cao nhất để đạt được các mục tiêu kinh tế tuần hoàn.
Một bước đi khác mà Tập đoàn đã thực hiện, đó là đầu tư vào công nghệ Rửa - Ép đùn - Ép phun để tái chế nhựa polyetylen (PE) và polypropylen (PP) để sản xuất pallet và thùng rác, đồng thời triển khai hệ thống quản lý tự động, số hóa.
Tận dụng thế mạnh của mình trong nghiên cứu, sản xuất và sáng tạo, THP đặt mục tiêu mang đến cho rác thải một cuộc sống mới bằng cách sử dụng rác thải để tạo ra các sản phẩm mà công ty có thể sử dụng. Đạt được mục tiêu này là một thách thức liên quan tới hầu hết các bộ phận tại THP.
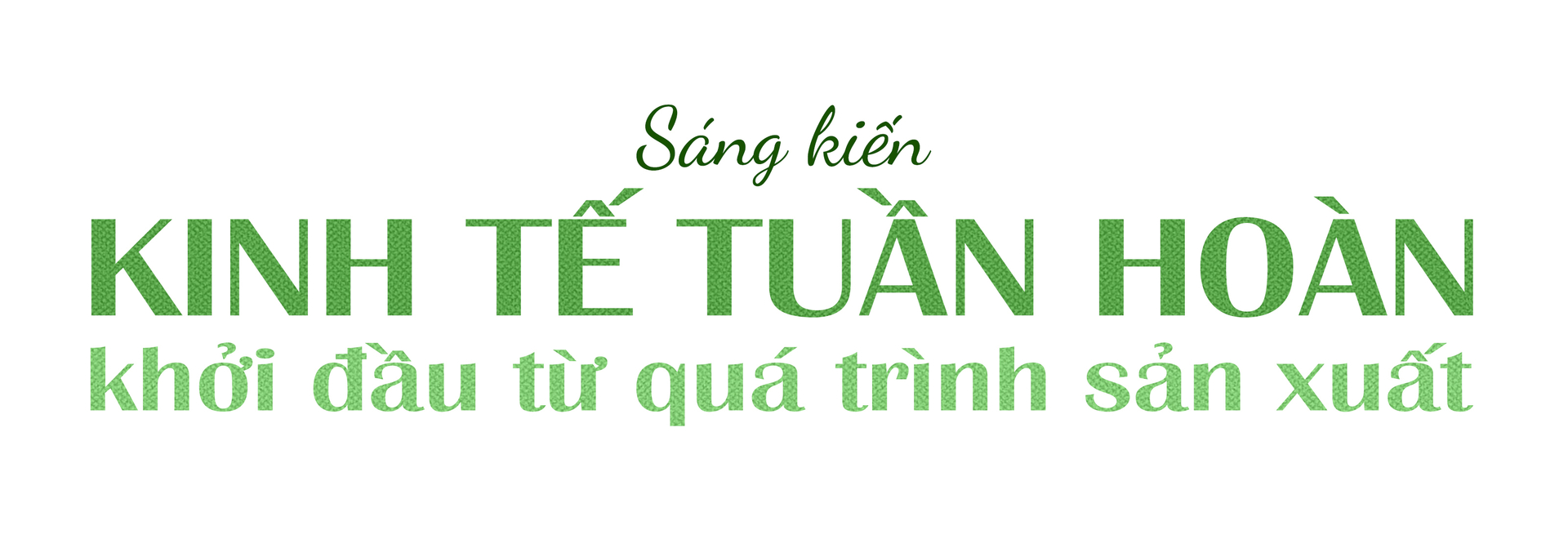
Vào năm 2013, THP đã triển khai dự án Giảm trọng lượng trong đó trọng lượng của mỗi chai nhựa được giảm từ 27g xuống còn 21,8g thông qua nghiên cứu, thiết kế và đổi mới. Công ty đã sử dụng máy móc tiên tiến nhất của châu Âu để tạo ra hiệu quả tổng thể về hiệu suất, giảm hao hụt trong quá trình sản xuất giúp tiêu thụ năng lượng điện và nước ít nhất. Năm năm sau, vào năm 2018, trọng lượng chai lại được giảm xuống còn 15,6g và 13,2g tùy loại sản phẩm. Hiệu quả về môi trường của sáng kiến này là rất lớn dù chỉ tiết kiệm được vài gam nhựa trên mỗi chai nhựa: Tính từ năm 2013 đến 2018, Tân Hiệp Phát đã cắt giảm được 34.000 tấn rác thải nhựa và trong 4 năm từ 2019 đến 2023, con số tiết kiệm được là 44.000 tấn, như vậy 9 năm qua, tổng cộng 78.000 tấn đã được cắt giảm.
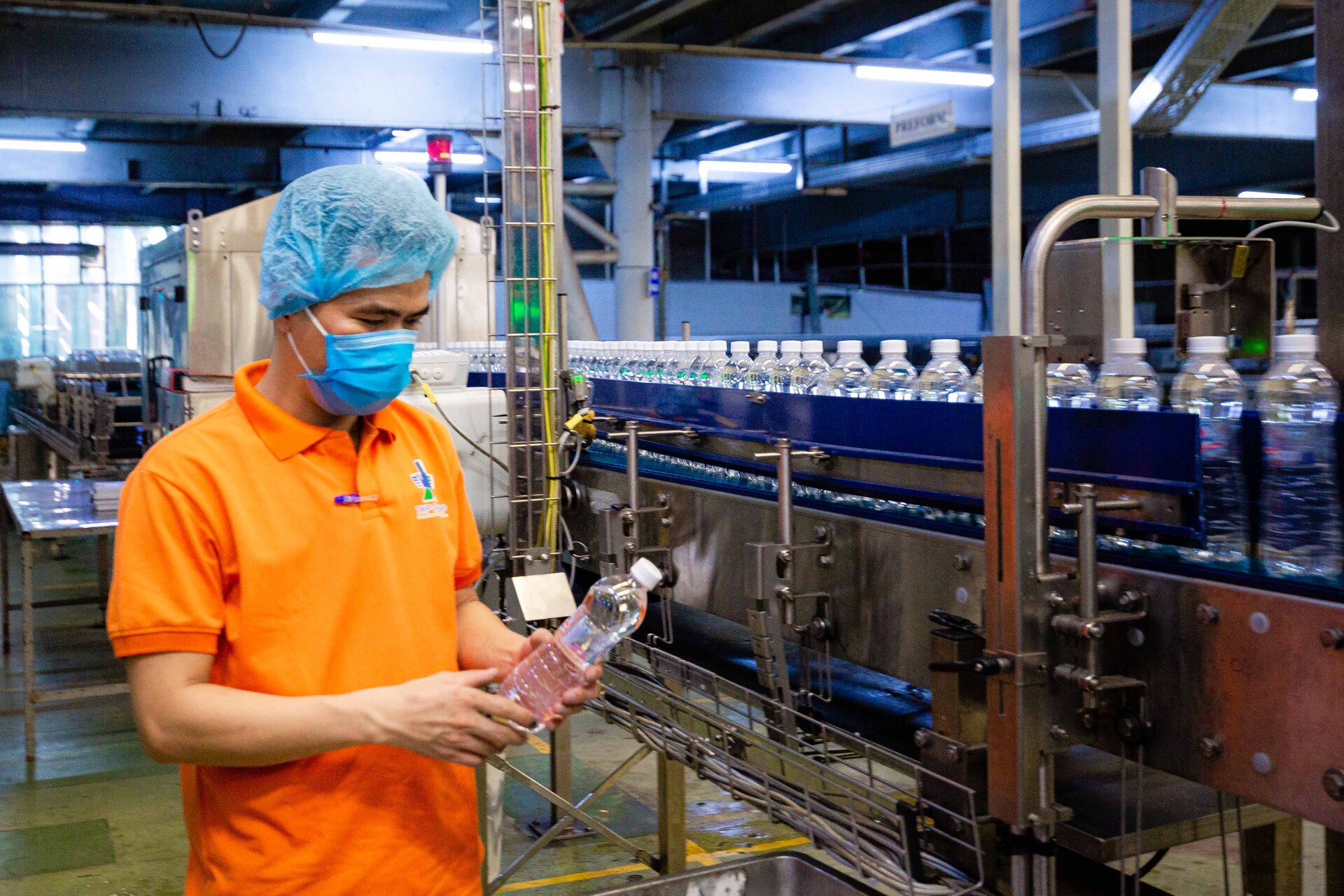
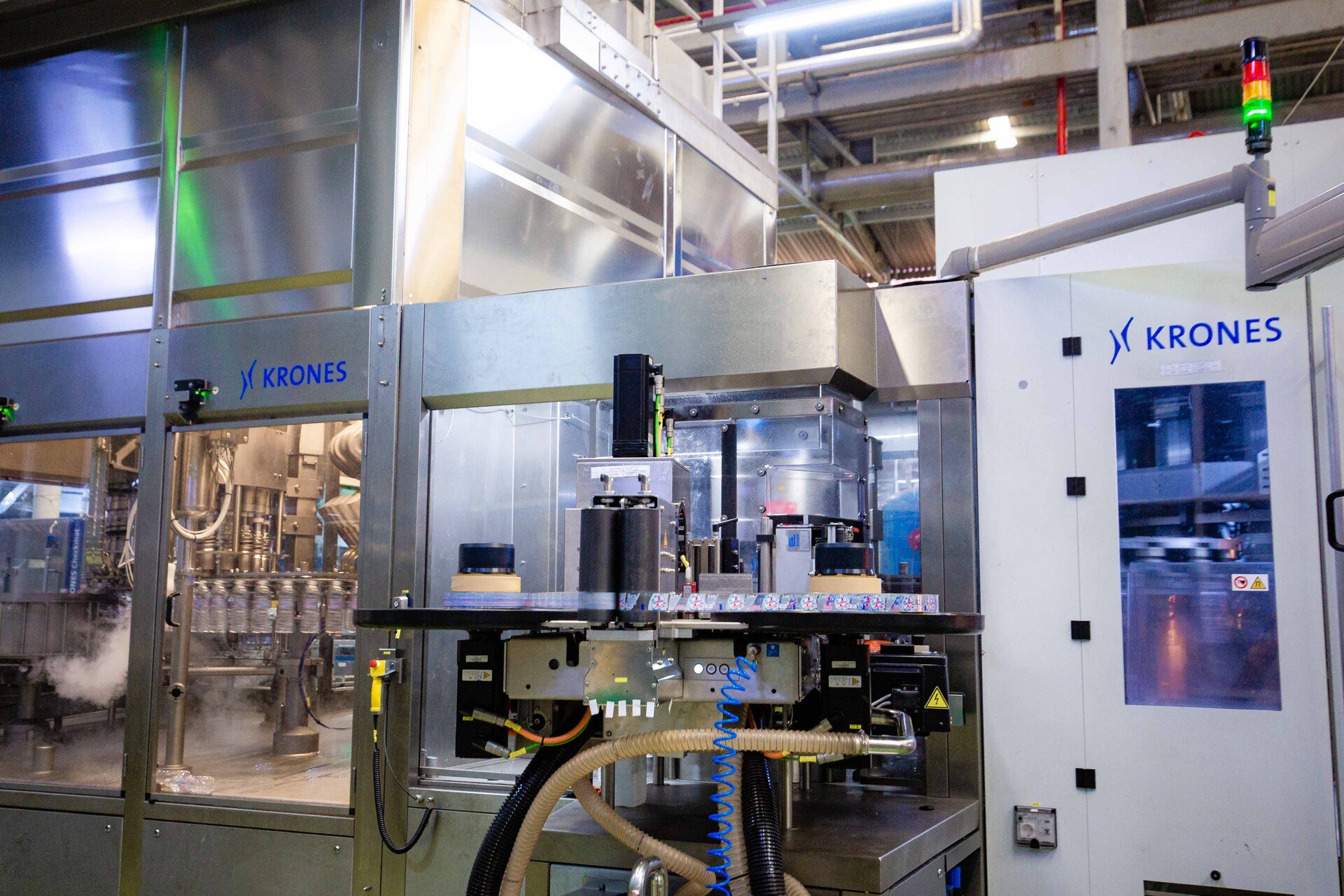

Tân Hiệp Phát sử dụng máy móc tiên tiến nhất của châu Âu để tạo ra hiệu quả tổng thể về hiệu suất, giảm hao hụt trong quá trình sản xuất, giúp tiêu thụ năng lượng điện và nước ít nhất.
Song song với đó, từ năm 2013, các loại màng co và túi PE được Tập đoàn tái chế 100% và tái sử dụng trong nhiều năm làm túi phục vụ nhiều mục đích như chứa đựng phôi (preform), nắp và túi đựng rác. Các màng co, túi PE và phụ phẩm trong quá trình sản xuất được thu gom và thông qua công đoạn xay và tạo hạt PE tái sinh. Qua công đoạn thổi, hàn, cắt bằng máy thổi màng hiện đại, các hạt nhựa tái sinh trở thành màng co để đóng lốc chai hay túi đa năng sử dụng cho 7 nhà máy của Tập đoàn.
Năm 2022, Công ty loại bỏ việc sử dụng thùng carton đối với nước tinh khiết Number 1 và thay vào đó chỉ sử dụng màng co PE làm từ hạt nhựa tái chế. Vào năm 2021, trong thời kỳ đại dịch COVID-19, Công ty đã bắt đầu vận hành các dây chuyền tái chế PP và Polyetylen tỷ trọng cao (HDPE). Công suất tái chế tối đa hiện nay là 300 tấn nhựa mỗi tháng. Dây chuyền sản xuất này nhằm sản xuất pallet nhựa từ phế liệu HDPE.
Quá trình sản xuất bao gồm ba giai đoạn chính:
Một là, đầu vào sản xuất là phế liệu nhựa HDPE/ PP/ PET (polyethylene terephthalate) được mua từ chuỗi thu gom phế liệu truyền thống. Phế liệu mua về sẽ được kiểm tra chất lượng đầu vào đảm bảo đáp ứng tiêu chuẩn chất lượng nguyên liệu của Công ty. Đầu tiên, phế liệu sẽ được nạp lên băng tải phân loại, đi qua máy dò để kim loại. Sau đó đi qua máy nghiền tinh, tại đây phế liệu được nghiền vụn bởi tác động cơ học và đạt kích thước lưới sàn lọc bên dưới. Tiếp theo, các mảnh nhựa được được chuyển vào bể rửa và tuyển nổi số 1 thông qua trục vít. Sau đó chuyển đến bồn rửa nóng có chứa chất tẩy rửa dạng kiềm để làm sạch các chất bẩn có thể hòa tan được.
Tiếp theo, các mảnh nhựa được đưa đến máy rửa siêu tốc có sự ma sát bề mặt mảnh nhựa để làm sạch các vết bẩn khó làm sạch. Sau đó mảnh nhựa được rửa tinh tại bể tuyển nổi số 2. Dòng mảnh nhựa sau bể rửa tinh được chuyển vào máy ly tâm tách nước. Tiếp theo là hệ sấy khí nóng với nhiệt độ 110-130oC để tách ẩm hoàn toàn đạt độ ẩm < 1%. Bước cuối cùng trước khi đóng gói là 2 máy tách bụi để loại bỏ nhãn/màng vụn, hoặc bụi cám để vảy thu được đồng đều.
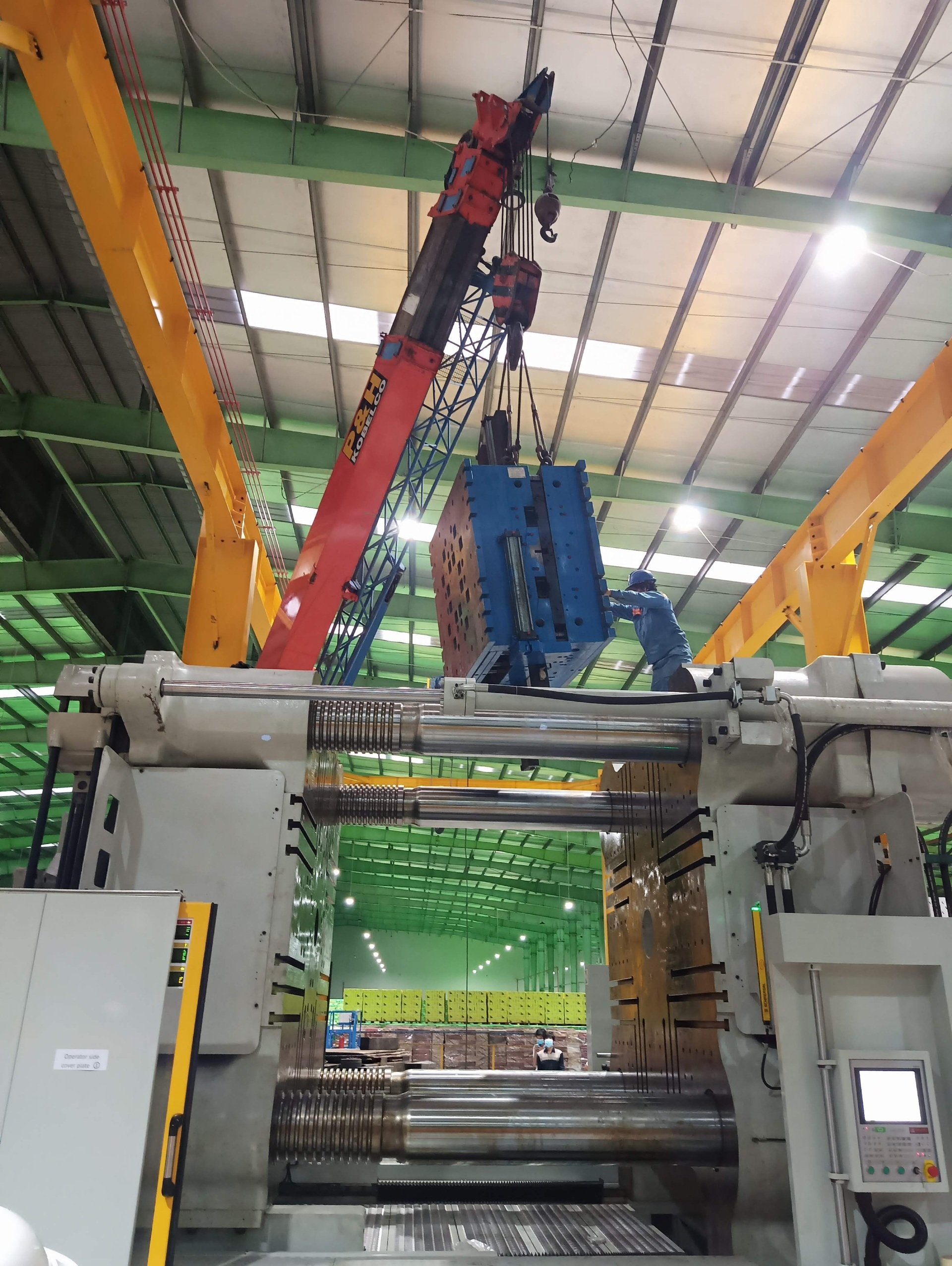
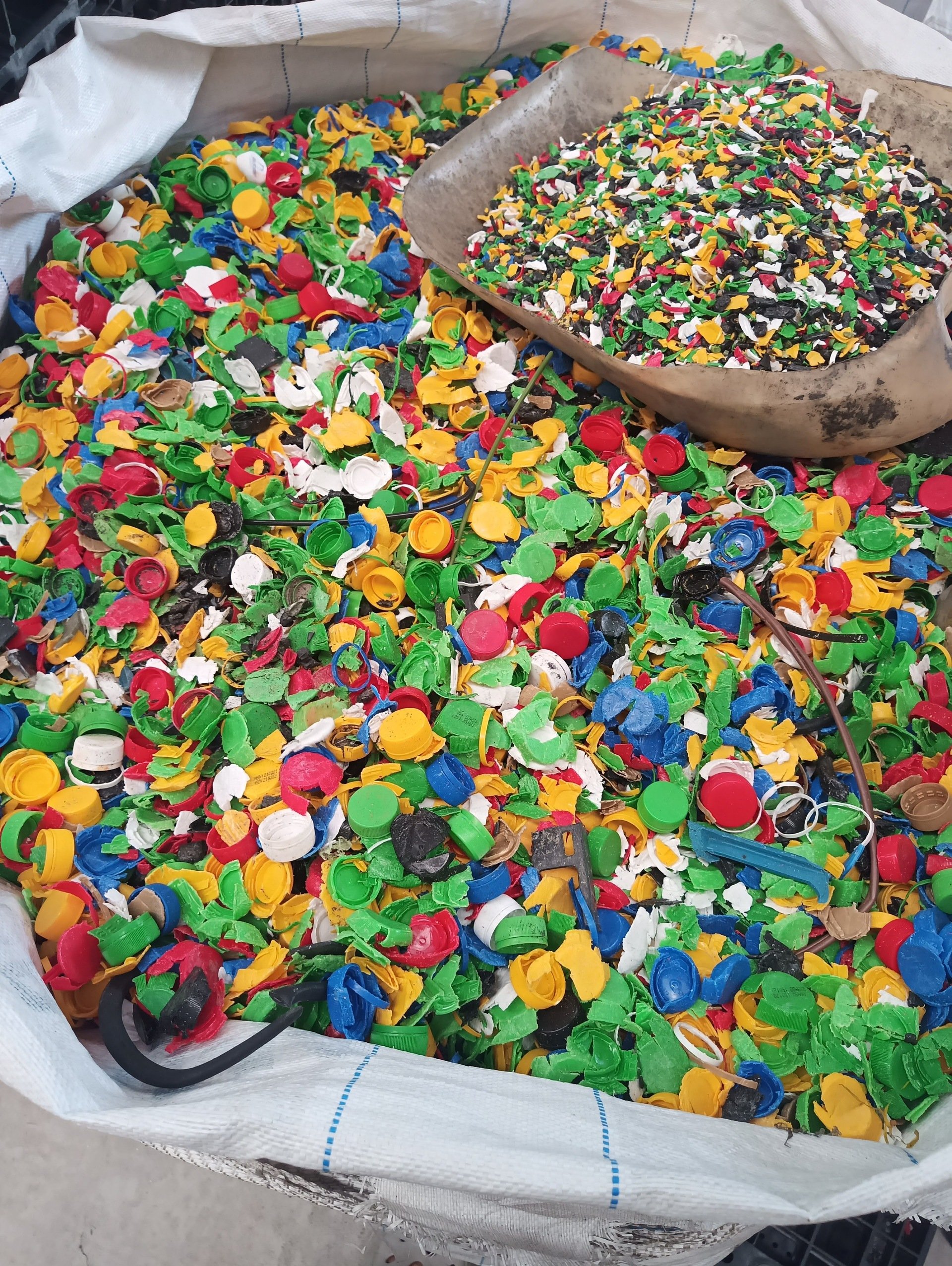
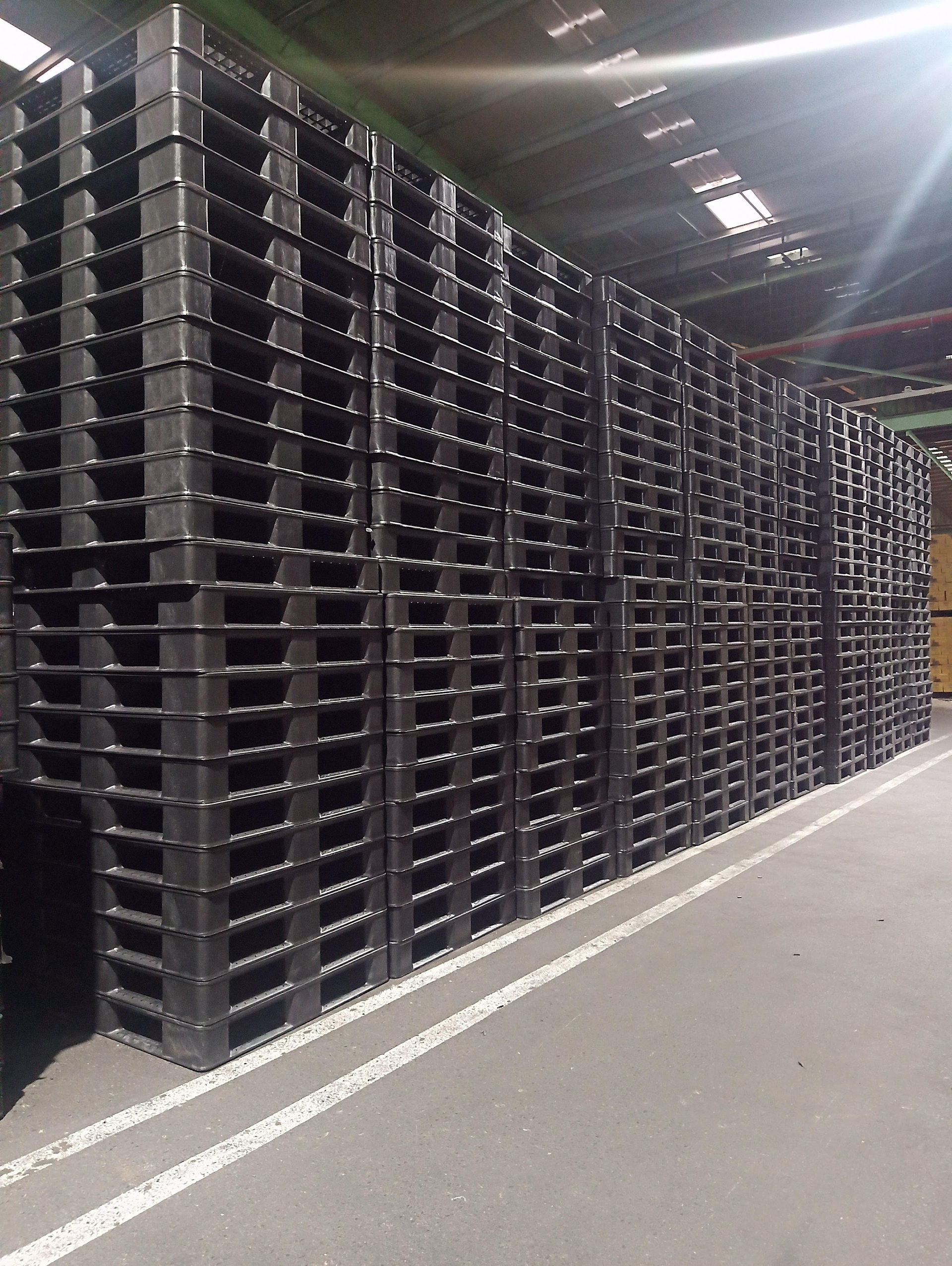
Tái chế nhựa tại nhà máy của Tân Hiệp Phát.
Hai là, sản xuất hạt nhựa HDPE tái chế. Ở giai đoạn này, các vảy nhựa được đưa vào máy ép đùn, để tạo hạt nhựa tái sinh. Máy ép đùn trang bị hệ thống hút chân không để loại bỏ các khí dư, độ ẩm trong vít có thể gây ra tình trạng hạt nhựa rỗng, bong bóng. Nhựa đùn ra được làm mát trên máng kim loại, và sau đó kéo qua hai quạt sấy khô trước khi đi vào máy cắt. Bên trong máy cắt, các đoạn nhựa dài được cắt thành hạt có kích thước nhỏ hơn 4mm. Các hạt nhựa tái sinh này được đi qua máy sàn rung để đảm bảo kích thước theo tiêu chuẩn nội bộ và hoặc tiêu chuẩn của khách hàng tiềm năng.Hạt nhựa tái chế được đóng gói và bảo quản để sử dụng cho quá trình sản xuất sản phẩm tái chế, thương mại hóa hoặc cung cấp cho các khách hàng.
Ba là, sản xuất pallet nhựa tái chế. Một tỷ lệ đáng kể của các hạt nhựa sau đó được sử dụng để sản xuất pallet nhựa tái chế. Dòng hạt nhựa đi vào vít đùn to thiết kế chuyên biệt để chạy 100% nhựa tái sinh, để hóa dẻo đồng nhất trước khi phun vào khuôn ép. Tại khuôn ép dòng nhựa lấp đầy bởi áp lực phun lớn và lực kìm khuôn lớn 30,000KN (~3000T). Sau đó, khuôn được giải nhiệt để sản phẩm được định hình trong khuôn. Khuôn được tách ra bằng lực đẩy tự động của giàn ejector và robot gấp sản phẩm ra khỏi máy. Pallet nhựa được kiểm tra và loại bỏ bavia để hoàn thiện sản phẩm và chất xếp lưu trữ theo quy cách được quy định nội bộ sau đó ứng dụng trong hoạt động chất xếp và vận chuyển các nhà máy.
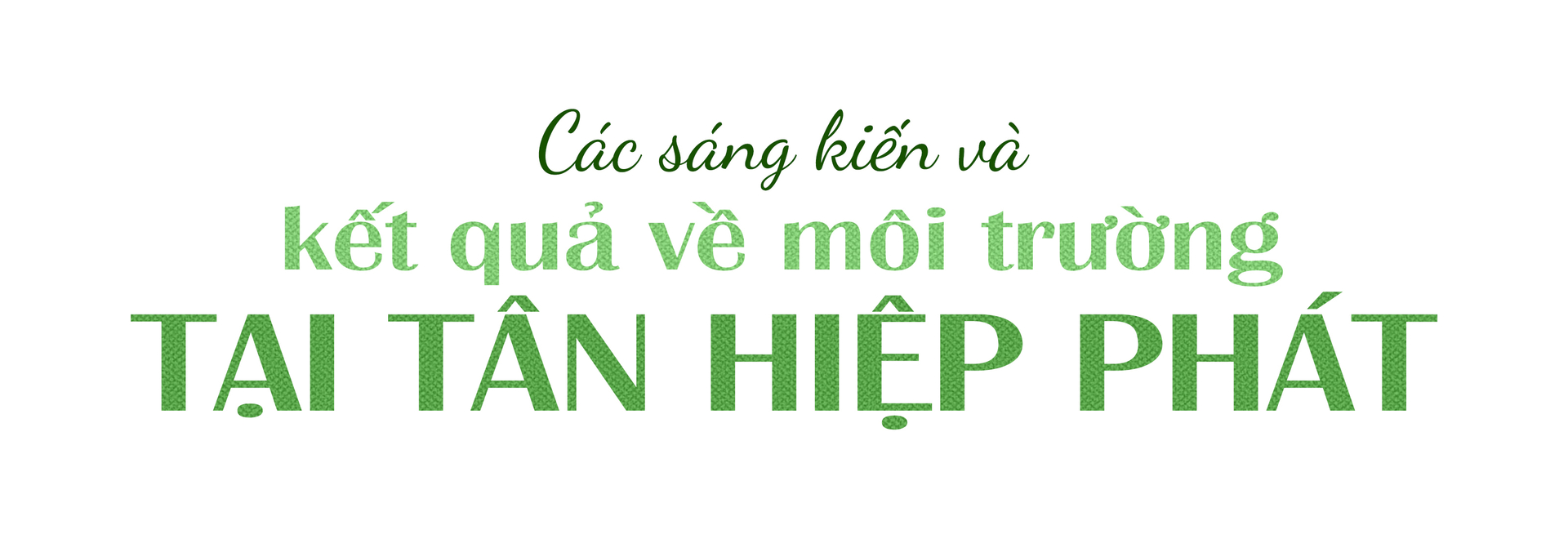
Kể từ năm 2013, THP đã thực hiện một số sáng kiến tái chế nhựa, đồng thời giảm lượng sử dụng bằng cách đổi mới thiết kế chai nhẹ hơn và sử dụng nhãn, màng đóng lốc mỏng hơn trong quy trình sản xuất. Mục đích tổng thể là giảm lượng nhựa nguyên sinh có nguồn gốc từ dầu mỏ như nhựa PE và PET trong các quy trình sản xuất của mình.
Như đã đề cập trước đó, trong 5 năm đầu tiên thực hiện các biện pháp bền vững hơn, Tập đoàn đã giảm hơn 34.000 tấn nhựa sử dụng (2013-2018). Trong 4 năm tiếp theo, tiếp tục giảm sử dụng 44.000 tấn (2019-2023).
THP đã mở rộng các hoạt động KTTH giúp giảm tác động đến môi trường và giảm KNK thông qua việc giảm sử dụng nhựa sử dụng một lần và tăng cường sản xuất các sản phẩm nhựa tái chế. Pallet và hạt nhựa tái chế được sản xuất từ hơn 3.500 tấn nguyên liệu PE và PP được thu gom từ thị trường trong năm 2022.
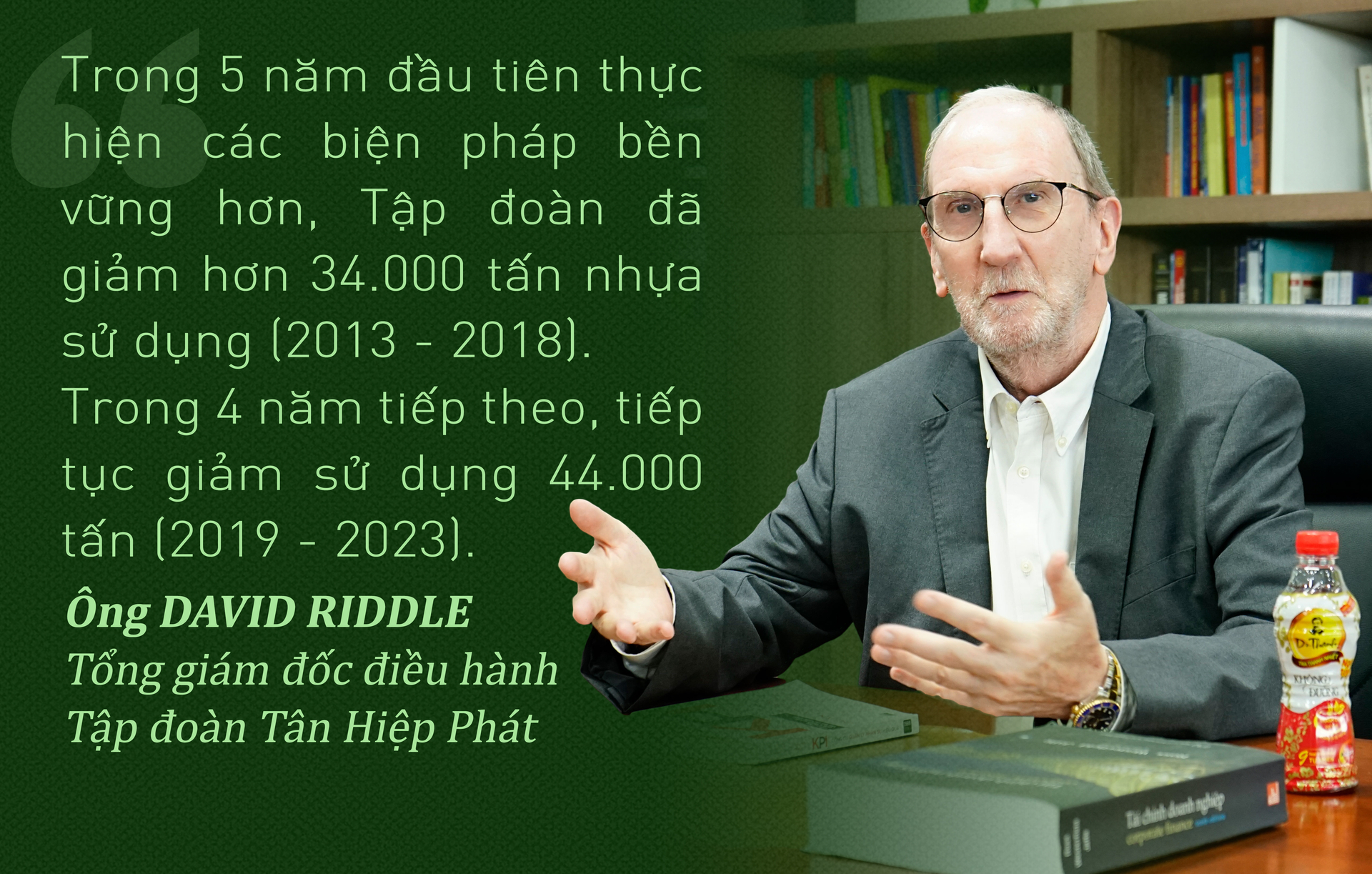
Sau mười năm triển khai mô hình 3R, từ 2013-2022, THP đã nhận thấy một số lợi ích đáng kể, cả trong việc đạt được các mục tiêu của nền KTTH và các lợi ích kinh tế cụ thể. Các tính toán cho thấy mức giảm mà Tập đoàn đã đạt được trong việc sử dụng vật liệu nhựa nguyên sinh có nguồn gốc từ dầu mỏ tương đương với việc giảm hơn 147.420 tấn KNK trong 9 năm qua.
Chất lượng nhựa mà THP sản xuất nội bộ từ các quy trình tái chế hiện đáp ứng các tiêu chuẩn nội bộ mà Tập đoàn đưa ra và THP cũng có thể thương mại hóa một số sản phẩm nhựa của mình bao gồm pallet nhựa và hạt nhựa tái chế. Điều này mang lại cho THP cơ hội không chỉ đạt được nền KTTH trong phạm vi Tập đoàn mà còn hỗ trợ các công ty khác đạt được các mục tiêu KTTH của riêng họ.
Mục tiêu KTTH tại THP trong tương lai: THP đặt mục tiêu cắt giảm hơn 112 nghìn tấn nhựa vào năm 2027 và tiếp tục mở rộng KTTH, chung tay cùng các doanh nghiệp tái chế nhựa khác.
Thông qua mô hình 3R, THP đang góp phần phát triển và hội nhập nền KTTH theo Đề án "Phát triển KTTH" ở Việt Nam được Chính phủ ban hành ngày 7/06/2022, đồng thời tạo cơ hội gắn kết với các đối tác, các đơn vị sản xuất trong và ngoài nước cùng tham gia để thúc đẩy phát triển mở rộng KTTH.
Việc triển khai mô hình 3R cũng giúp tăng cường sự gắn kết, sự tự hào của cán bộ nhân viên về một Tập đoàn đã luôn đặt trách nhiệm xã hội là một phần trong các giá trị cốt lõi.
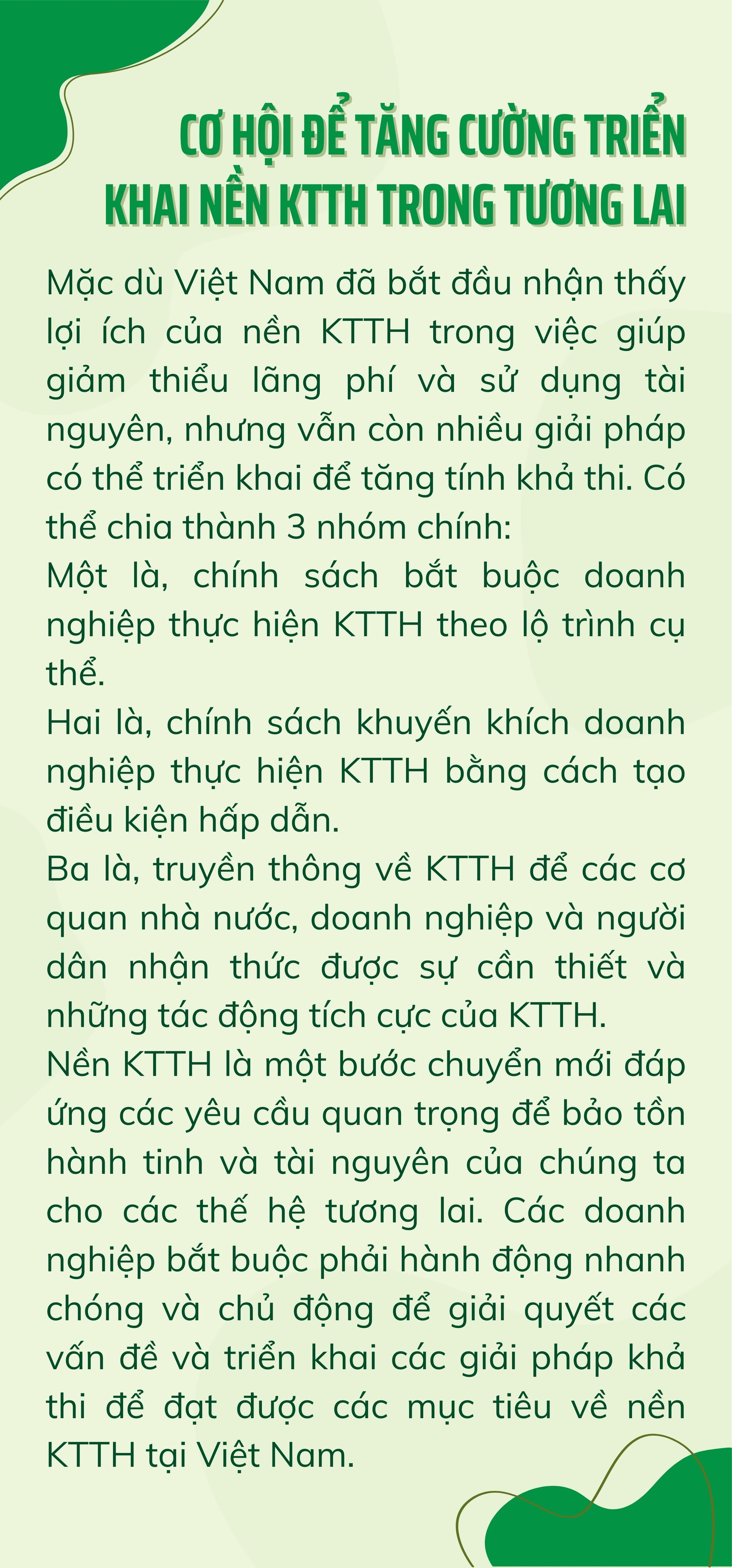